TWPC, a Cat 2 Nuclear Facility, is the Oak Ridge Reservation (ORR)’s center for the management, treatment, packaging and shipment of Transuranic (TRU) waste legacy inventory.
Our six years as the prime contractor required comprehensive expertise in disciplines ranging from hazardous materials management, remediation, and waste management, to conduct of operations (CONOPs), engineering, and security. Our primary role was to disposition the U.S. Department of Energy (DOE) Oak Ridge Environmental Management (EM) legacy TRU waste inventory through segregation of non-conforming waste, subsequent treatment, interim storage, containerization, and transport for disposal.
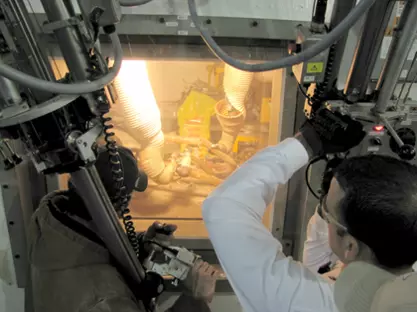
Waste managed at the TWPC is in storage or generated by ongoing activities, either on the ORR or other DOE sites. Project scope included managing an inventory of more than 5,000 waste containers.
VNSFS processes and disposes of low-level waste (LLW), mixed low-level waste (MLLW), and hazardous or industrial waste resulting from contact-handled TRU and remote-handled TRU waste processing. We also manage any industrial or hazardous waste generated by the project. All wastes are processed and packaged for compliant disposal in offsite radioactive waste repositories – Waste Isolation Pilot Plant (WIPP) for TRU wastes and the Nevada National Security Site (NNSS) or other sites or other DOE sites for LLW and MLLW.
Throughout its tenure at TWPC, VNSFS has shipped more than 1,200 drums of TRU waste, including more than 500 drums of TRU soils. VNSFS also packages and ships LLW radioactive and MLLW waste for disposal at the Nevada National Security Site.
Some specific highlights of our enhanced facility operations include:
Designed/built/operated a Cask Processing Enclosure to address a unique problem associated with groundwater infiltration into containers that had been stored underground and to increase life cycle and reliability of high-maintenance equipment. This resulted in ~$20M in savings; two-year schedule reduction and increased processing rates by ~70 percent.
Developed a data-driven change-out program for manipulators and robotics using predictive modeling of failure rates of manipulators versus position in hot cell, waste type and other variables resulting in approximately 20 percent increase in hot cell throughput, and manipulator downtime was significantly improved.
Implemented automated field data-logging platform via iPads that allows rapid notification of potential hazards to workers on next shift via scanning barcoded SS SSCs.
Designed/installed a DVS to allow safe opening of overpacked CH waste drums which provided ~$250,000 of cost savings to DOE; reduced schedule by five months; and produced a stable, high-volume feedstock stream.